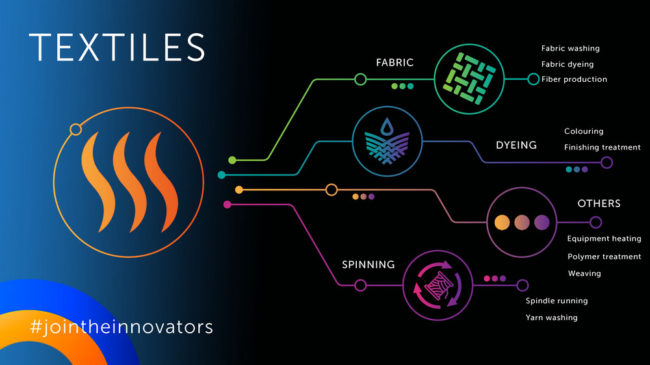
Steam utilization in the textile industry – infographic. Courtesy: Byworth Boilers.
Recycle/reuse of cooling water and condensate water as boiler feed water
-
Description
-
Effects & Applicability
-
Operation data
-
Economics
-
Implementation
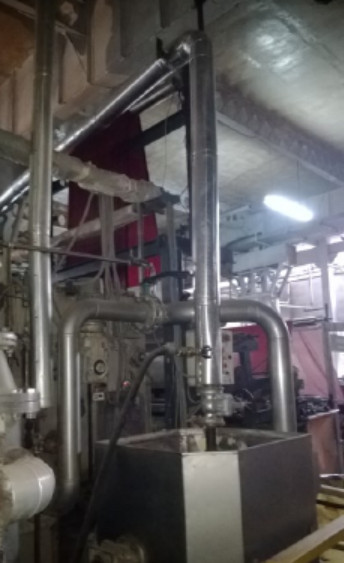
Reuse of Recovered Condensate at Other Machines (Source: GIZ-IGEP and GCPC team)
Cooling water and condensate water are non-process water uses. Many cooling water systems are operated on a once-through basis. Condensate water includes water from heat exchangers in dyeing machines, drying ranges, cooling cans on continuous ranges, while cooling water includes hot water from jet dyeing machine and compressors (if water cooled). In the knit industry for example, the amount of cooling water utilized in the process is equivalent to 13% of total fill and rinse water. Traditionally, jet dyeing machines are equipped with common heat exchangers that are used for both heating and cooling which is normally drained with other effluent and thus increasing fresh water consumption as well as effluent quantity & load at effluent treatment plant.
Recycle/reuse of cooling water and condensate water as boiler feed water resulted in the following benefits:
- Boiler feed water consumption reduction: 100% (depending on recovered quantity).
- Recovery of energy in form of heat from hot water: 15% minimum
- Reduction in boiler emissions.
- Reduction in waste water generation (quality & quantity).
This technology does not affect chemical use, but because effluent volume is reduced, the concentration of chemicals in the effluent will increase.
The technique is applicable to both existing and new installations. In new installations condensate recovery system and a steam boost system as a measure is considered to save water and improve energy efficiency.
The total boiler feed water is being now catered by recovered condensate & cooling water amounting to 50 KL per day.
Both the cooling water and the condensate is recovered completely from jet dyeing machines and reused as boiler feed water in Rinkoo Processors. While cooling water from jet dyeing machines is reused as process hot wash water on soft flow dyeing machines, RFD (Ready For Dyeing) machines, etc. in Komal Texfab.
Capital costs for implementation was Rs. 3,00,000, operating costs includes the pumps operation of 10 HP for transfer amounting to Rs. 3,13,000 per annum, resulted in saving of Rs. 33,00,000 per annum with payback period of 3 months (Rinkoo Processors). Capital costs for implementation was Rs. 11,00,000, while operating costs includes the pumps operation of 10 HP for transfer amounting to Rs. 1,96,000 per annum, resulted in saving of Rs. 12,12,000 (Rs. 5,94,750 fuel cost + Rs. 6,17,760 fresh water pumping cost) per annum with payback period of 13 months (KomalTexfab).
Contribute to overall reduction of water and energy consumed. In order to allow full exploitation of the benefits achievable with the new advanced washing machinery, the implementation of the low-technology measures is fundamental. The main driving forces for the implementation of the described techniques are the increasing cost of water supplies and waste water treatment, and the desire for increased productivity (in the case of new highly efficient washing machinery).