Different Production Steps Called “Textile Pipeline”
-
Yarn Production
-
Weaving
-
Knitted Fabrics
-
Nonwovens
-
Wet Processing

VARIOline - the variable opening and cleaning concept from Rieter
Machinery for spinning preparation forms the fibres into a sliver, thereby preparing them for the spinning procedure. This includes bale opening, cleaning from impurities, reducing the tufts to a minimal size as well as the blending of different raw materials. For these purposes, one needs bale openers, cleaners, blenders, cards, drawing frames and combers. Different machine configurations and techniques come into operation, depending on the desired yarn properties and the raw materials in use.
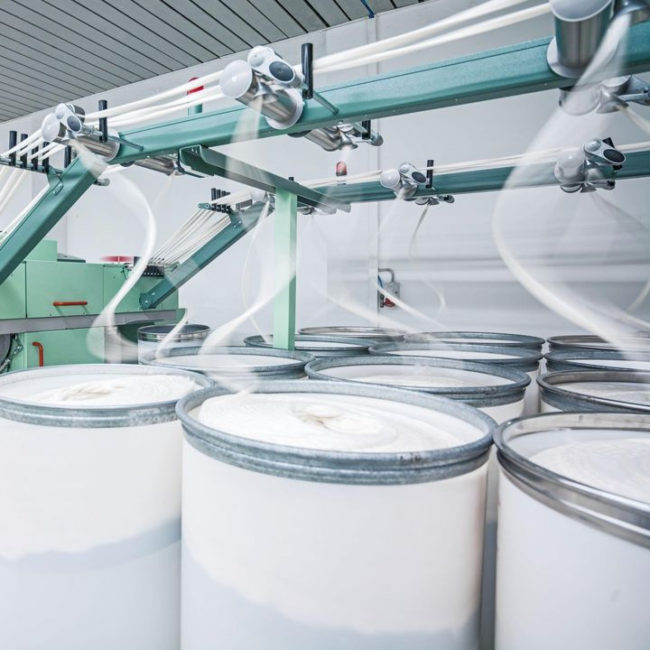
Rieter's comber is highly economical
For the actual spinning process, there is the conventional ring spinning method on the one hand and there are newer methods such as open-end rotor spinning on the other.
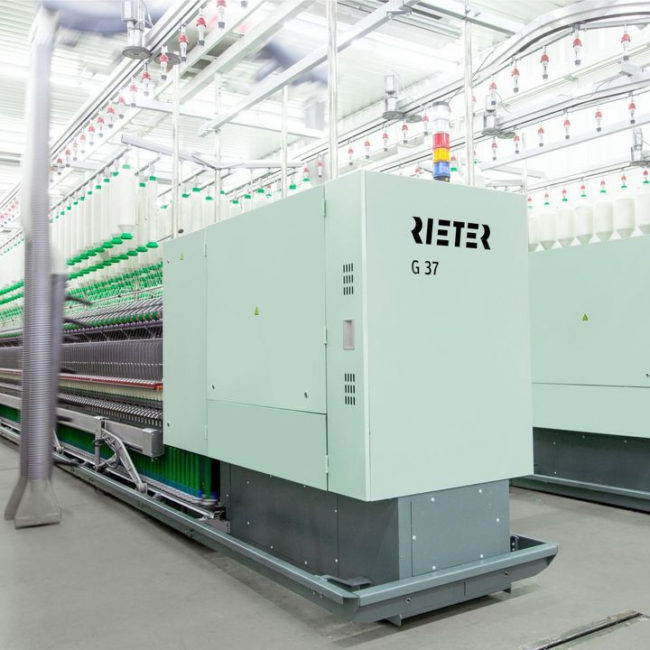
The ring spinning Rieter m/cs. produce high-quality yarn reliably and economically
Ring spinning combines three processes: flyer, ring spinning and winding. In ring spinning, a bundled fibre structure is drawn up to 50 times, then twisted and finally wound. In open-end spinning, however, the bundled fibre structure is undone and the individual fibres are tied to a rotating open thread end.
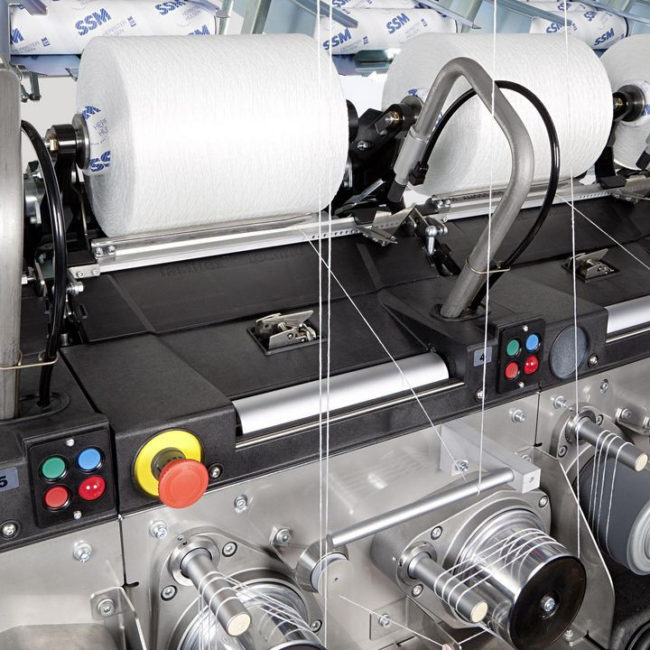
Air texturing and false twist texturing machines from SSM
In man-made fibre and filament production, the spinning process is based on the following principle (simplified description): a spinning pump feeds the spinning jet (spinneret) with a liquid high-polymer com- pound which is pressed through the spinneret’s openings at a pressure of up to 450 bar. A chemical reaction or solidification and drawing make the fibre assume its final shape and orientation when it leaves the spinneret. Depending on the purpose, the diameter of the spinneret is between 0.05 and 0.5 mm, with a tolerance of no more than +/- 0.002 mm. By crimping, texturising machines give filament yarns volume and elasticity. In order to be blended with natural fibres, plain filaments are cut or broken into staple fibres.
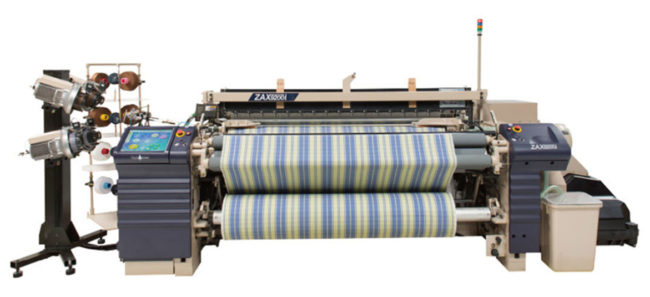
Tsudakoma's best-selling air jet loom the "ZAX9100 Professional."
Weaving is the predominating method used for producing textile fabrics. A weft yarn is merged perpendicularly with warp yarns that are aligned in the direction of the production run. But before the actual weaving process can begin, a number of preparations need to be made. In particular, these include winding (spooling of yarns onto conical or cylindrical bobbins), doubling (twining of several yarns), twisting if necessary, warping (different methods of spooling the warp yarns) and sizing (pre-treatment of the warp yarns in order to improve their processing during the weaving process). These jobs are done by special machines, classed as weaving preparatory machines.
There are several ways of transporting the weft yarn through the shed:
A weaving shuttle containing a yarn bobbin is driven through the shed (shuttle weaving ma- chine, outdated technology, prototype of mechanical weaving), but applied in a more modern way, e.g. for weaving paper machinery fabrics and other technical textiles.
Modern weaving machines operate on the following principles:
- The weft yarn is driven through the shed by a projectile (gripper shuttle loom) or
- a rapier feeds one end of the yarn to the middle of the shed and passes it on to a second gripper which transports the yarn to the end of the shed (rapier weaving machine).
The weft yarn is transported through the shed by means of air pressure or a jet of water (jet weaving machine
The application area for woven textiles ranges from clothing across carpeting to the production of technical textiles.
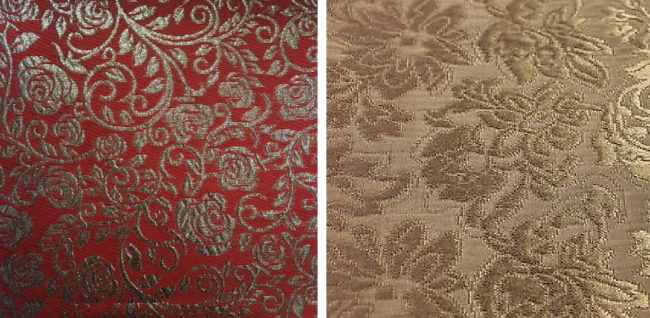
Jacquard Woven Fabric
Jacquard weaving machines can create different patterns by lifting single or whole groups of warp yarns.
The warp yarns can be lifted individually via so-called harness cords, making it possible to produce any pattern.
Textile fabrics can also be formed by producing knitted fabrics or hosiery. The classical application areas are clothing (pullovers, stockings, underwear, sportswear, etc.) as well as home and household textiles (curtains, table cloths, bedcovers, etc.) production. But knitted fabrics have also gained importance in the field of engineering, e.g. as geotextiles, filtration fabrics, insulation material, in medical engineering and other areas. Knitting machinery is divided into circular knitting machines and flat knitting machines.
Flat knitting machines allow for knitting and making up at the same time; it takes only about half an hour to produce a seamless pullover.
Warp knitting machines use another principle. Several threads are fed to needles that move simultaneously and at the same time formed into loops. That way, up to 80 metres of knitted fabric can be produced per hour.
As the name suggests, nonwovens are textiles that are not woven, but made of fibres or continuous filaments. They are produced in three steps (web formation, bonding, finishing), for which German textile engineering supplies a complete range of machinery. On main technology in order to produce nonwovens, the fibres need to be prepared (opened, cleaned, mixed). Then the fibres are formed into a web which can be up to 5 metres in width, e.g. on a nonwovens card. Multiple and cross layering of the fleece results in broader and more equal webs with defined fibre orientation.
This intermediate product is bonded either mechanically by needles or jets of water, chemically by spraying or soaking the web with bonding media, or thermally by heat bonding. In order to produce spun- bonded or melt-blown nonwovens, the polymers are forced through spinnerets, and in one go the emerging filaments are drawn off aerodynamically, mechanically or electrostatically and piled onto a filter band.
Until 2022 the global production of nonwovens will in- crease with annual rate of around 6.3 % to over 13.6 million tons (Source: Smithers Pira, Marktbericht 1.06.2017); (2000: 3,2 Mio. t, 2009: 7,1 Mio. t, 2017: 10,1 Mio. t). The greatest share in the market is, so far, represented by nonwovens for industrial and medical engineering purposes, followed by nonwovens for home and household uses and applications in the building branch. Accordingly, suppliers to the automotive industry or manufacturers of medical and hygiene nonwovens are important consumer branches for the manufacturers of machinery and accessories for the nonwovens.
Washing, Bleaching, Dyeing, Printing and Finishing
This machinery is used to provide fabrics, knitted fabrics or nonwovens with specific properties for particular purposes. Depending on whether water is used or not, one distinguishes between dry or wet finishing. To begin with, all residues from preceding processes are washed out of the fabrics. Cotton fabrics are carbonised and often mercerised, then bleached. Thereafter, fabrics are printed, dyed or coated. By “finishing”, the textiles are then equipped with the desired properties, e.g. certain surface effects.