Uzbekistan is modernizing its industry
Uzbekistan is developing into an international industry hotspot. Numerous expansion projects are firmly planned. The government is pursuing a very ambitious goal: The annual domestic volume of cotton fibers (1.1 million tons) is to be completely processed into semi-finished and finished products by 2023 at the latest. Central industry concepts for the years 2020 to 2025 include more than 200 projects worth more than 3 billion US dollars (US $).
The number of cotton-textile clusters expanded from 15 to 97 between 2018 and 2020. The trend will continue in 2021: US $ 400 million to 500 million will flow into the expansion and modernization of the textile and clothing industry. Industry output is expected to reach around US $ 15 billion annually by 2025 (2019: US $ 4.3 billion).
The Government of Uzbekistan (GoU) abolished state production quota for cotton in 2020
In February 2020 the Government of Uzbekistan (GoU) announced something, which many country’s observers considered impossible even only several months ago – it announced the abolishment of the state production quota for cotton in 2020, with the decree and the resolution issued in early March 20202 . This means that 2019 was the last year in the history of Uzbekistan when a cotton production target was set by the state and a wide range of administrative and legal measures were taken to meet it. This decision has a wide-ranging effect on Uzbekistan’s socio-economic development, including on the elimination of forced labor use in cotton picking, a long-standing issue which has been difficult to fully resolve3 . The decision to abolish production quota was largely possible due to the rise of private sector cotton-textile clusters, which now dominate cotton production and ensure a transition of the cotton value chain from plan to market. But their roles, achievements, and future are still contested.
Cotton-Textile Clusters
The Government of Uzbekistan (GoU) carried out the largest reforms in 2017-2019 which included promotion of private investments in cotton value chains through cotton-textile clusters. Starting from 2020 the GoU allowed farmers/clusters to determine the total cotton growing area and also the use of specific “cotton varieties”in various parts of the country. Earlier, these decisions were taken by government authorities.
The clusters were created on a first-come-first served basis. Textile enterprises initiate a creation of clusters by submitting an investment proposal. Their final approval is made by the Cabinet of Ministers. Priority is given to investment proposals of textile enterprises with deep processing facilities, commitment to invest in the support to farmers for increasing yields, improving cotton quality, enhancing soil fertility and water management, and adopting mechanization. The number of cotton-textile clusters increased exponentially, from 15 in 2018 to 75 in 2019.
Most clusters work with farmers through “contract farming” arrangements. Many of them have leased land for “direct farming”, about 10-20 percent of total cluster area. Only 5-6 clusters have the most land area under direct farming, so the vast majority of clusters work with farmers. In 2019, the cotton-textile clusters operated in 86 districts on 63 percent of cotton growing areas. They produced 73 percent of total cotton output. Their number is expected to grow in the coming years. Contract farming is an arrangement, under which cotton is produced by farmers and sold to cotton processing/textile enterprises, which establish cotton-textile clusters. Direct farming is an arrangement, under which cotton/textile enterprise leases farmland from the state and produces cotton itself by hiring wage workers.
Contract farming vs Direct farming
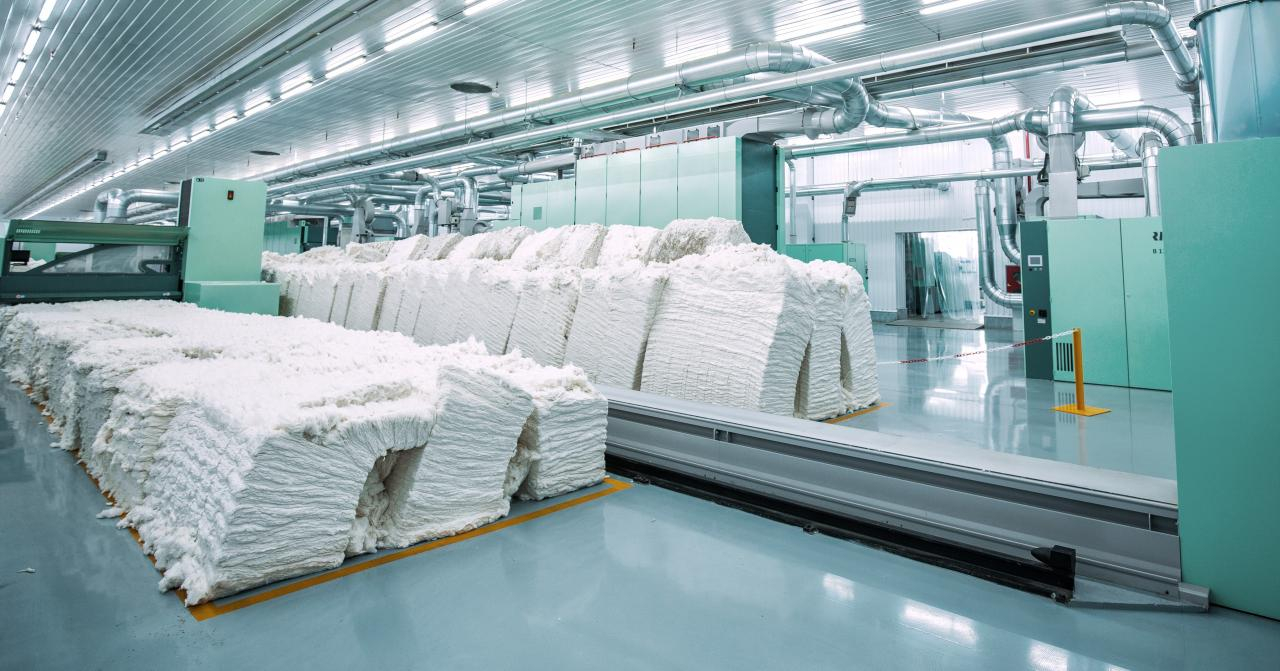
Khantex Group’s Cotton and Textile Cluster: Khantex Group harvests cotton grown under the hot sun of Andijan in their own agricultural fields using innovative methods and water-saving technologies to produce the highest quality and environmentally friendly fabrics from natural cotton fiber.
In 2019, the areas with cotton clusters generated higher cotton yields than the areas without clusters. Moreover, more than 40 districts with clusters reported the cotton production higher than in the last ten years. This is a big achievement for Uzbekistan, a country with limited land and water resources. The average raw cotton yield of clusters was 2.9 tons/ha (This is still a low yield in the global perspective. Cotton exporters, as Uzbekistan, achieve higher raw cotton yields: USA –3.1 tons/ha; Egypt –4.4 tons/ha; Turkey –5.3 tons/ha; Brazil –5.6 tons/ha; and China –5.8 tons/ha.), which was 0.53 tons/ha higher than outside of clusters and 0.88 tons/ha higher than the average in 2018. In 34 clusters, the yield was above 3.0 tons/ha, and in 9 clusters –above 3.5 tons/ha.
Achieving the yield increases has been a result of significant private investments in modern technology adoption and compliance with good agricultural practices. Many clusters, mainly on land leased for direct farming, have analyzed their soils and updated agro-technological maps on the area of 149,200 ha. They report to have adopted organic fertilizers (138,200 ha), deep ploughing (167,800 ha), drip irrigation (9,400 ha), and laser leveling of fields for more efficient seeding and water management (10,100 ha). These are all modern technologies, which were brought to Uzbekistan and adopted under the cluster model, albeit at the low rate, given that in 2019 the cotton growing area under clusters was 0.6 million ha.
File photo of Uzbek President, Shavkat Mirziyoyev, visiting Chust Textile in February
The Chust Textile is organized in Namangan Free Economic Zone. 1,300 people work in two complexes of the factory. The company, based on orders, is capable of producing a full range of clothing. In 2020, about 2 thousand tons of fabrics and 5.2 million units of finished knitwear were produced. Goods worth more than $9 million were exported to Italy, Russia, Kazakhstan and Tajikistan. Exports are expected to reach $12 million this year.
The total cost of the Chust Textile project is about $12 million. It will be implemented in three stages. With full capacity, the enterprise will produce 5,000 tons of fabric and 15 million units of finished products per year. It is planned to increase the number of employees to 2,200 people.
Private and public investments have led to a significant increase in the export of higher value-added products. More importantly, the export is shifting from low-value yarn to higher-value textile products.