Creating Value with Biomedical Textiles : Leads to Innovative Quality Practices
By Carola Hansen, Business Manager for Dyneema Purity® fiber of DSM, and Kevin Johnson, Director of Quality Assurance and Regulatory Affairs, Biomedical Structures LLC
Over the last few years, much of the innovation in the medical device industry has been fueled by advancements in fiber and other textile technologies specifically designed for use inside the human body. These medical textile breakthroughs have supported a broad array of implantable devices ranging from vascular grafts and surgical mesh to heart valve components and orthopaedic sutures to fabric scaffolds designed to aid in tissue engineering. The fabrics these applications are built upon help deliver more life-like products with the potential to perform better, last longer, and increase comfort in the body – all of which can potentially significantly improve outcomes for patients.
Medical-grade Materials —The Fabric of the Future
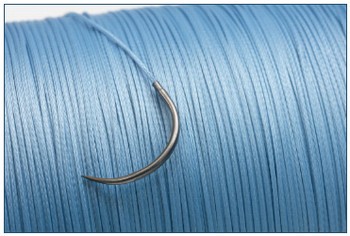
To fully capitalize on new materials for device applications, it’s critical for textile developers and yarn manufacturers to make quality their No. 1 priority.
These advantages, along with the growing concerns around more traditional implantable materials such as metal, are causing medical device companies (MDCs) to consider textiles for more device projects than ever before. But as demand for medical textiles grows, so too does the concern about the quality of these materials and the controls implemented by the companies that process them. Many traditional materials developers and textile manufacturers, seeing a promising business opportunity, are attempting to expand into medical textile development and processing, often without the necessary medical focus or expertise.
While MDCs’ interest in and reliance on these innovative new materials has increased exponentially over the last decade, they nevertheless have only scratched the surface of their potential in device applications. To fully capitalize on them, however, it’s critical for textile developers and yarn manufacturers to make quality their No. 1 priority so that evolution is not hindered or slowed by concerns about these promising materials’ performance. MDCs attempting to manage the unprecedented regulatory and economic challenges of the current environment, and simultaneously trying to meet growing surgeon and patient expectations, have to carefully balance investment in new technologies with intensive risk mitigation. Manufacturing partners that fail to meet the highest quality standards won’t just compromise their own business prospects, but also will hamper the development of one the most exciting industries within the med-tech sector.
As partners to the world’s most innovative MDCs, DSM and Biomedical Structures LLC are acutely aware of the challenges associated with med-tech development and are intently focused on the development and promotion of the quality practices for materials that not only support the successful commercialization of groundbreaking textile-based medical devices, but also raise the bar for the entire medical textile industry.
That top-tier quality management is so top of mind for MDCs today is hardly surprising. With aging populations increasing product demand, economic volatility tightening margins, and political reforms heightening regulatory oversight, MDCs are under increasing pressure to bring innovative, better-performing products to market quickly and successfully.
To help MDCs better manage today’s highly complex, high-stakes commercialization process, their partners must be well positioned to help them mitigate risk and minimize cost by engaging in the quality practices that will support MDCs in meeting their design specifications. Beyond the design spec, the device must ultimately pass biocompatibility tests and clinical studies and all the many other complex aspects of gaining regulatory approvals. But the obligation doesn’t end there, of course. To help ensure MDCs maintain their reputations in the industry as quality manufacturers, partners must also adhere to the practices that maintain the quality of the device over the long haul and help MDCs to avoid issues that could lead to product recalls or other adverse events.
A Quality Device Requires Quality Ingredients
Passing the biocompatibility tests at the end of the process depends primarily on two factors: the manufacturing process and the material chosen at the beginning of the design phase. And the ultimate quality of an implantable medical device utilizing fiber components relies first and foremost on the quality of the fiber it is built upon.
One fiber that has been attracting the attention of MDCs for device projects utilizing medical grade fibers is DSM’s Dyneema Purity® fiber, which is a UHMWPE fiber designed for use in the human body. The fiber possesses unique properties that help enable MDC designers to meet the market’s demand for higher-performing implants that are stronger, smaller and last longer. For example :
- Dyneema Purity® fiber is not only 15 times stronger than cable steel, but is also soft and highly pliable, which can improve comfort and compliance.
- Dyneema Purity® fiber’s resistance to fatigue and abrasion are advantageous in vascular applications that require thin structures, lowering the risk of complications due to internal or external stressors.
- Dyneema Purity® fiber’s near-zero stretch enhances fixation in orthopedic applications, such as knee and shoulder arthroscopy and also adds value to non-compliant balloon catheters.
Equally important, however, is the fact that Dyneema Purity® fiber is a raw material specifically designed for applications in the human body during surgery or over the longer-term lifespan of an implant. And unlike many textile developers, DSM, which makes Dyneema Purity® fiber and other highly advanced, innovative biomaterials, was formed with a specific focus on materials for medical applications. The Dyneema Purity® fiber has been through extensive biocompatibility and hemocompatiblity testing and has a Master File on record with the FDA, which can give MDCs a critical advantage in navigating an increasingly rigorous regulatory process to bring new products to market.
Dyneema Purity® fiber’s heritage as a medical-grade material demonstrates DSM’s commitment to the medical application market through its focus on meeting challenging material requirements. The company invested in clean-production capabilities and quality systems at its Heerlen, NL facility, to create a medical-grade UHMWPE fiber. One of the earliest successful collaborations was with an orthopedic sutures manufacturer that sought to maintain its competitive dominance in the field of rotator cuff repair, where uncompromising strength and performance were critical. Today, DSM’s Dyneema Purity® fiber is the gold standard in many high-strength sutures used in sports medicine applications.
DSM stands ready to help innovative device designers improve performance in a variety of existing and emerging application areas, and growing demand has prompted the company to expand its production of Dyneema Purity® fiber to its Greenville, NC, facility. Designed to best-in-class quality and manufacturing specifications and guided by customer input, the facility supports a world-class medical manufacturing capability and is set to begin releasing product in the first quarter of 2012. Like all of DSM’s facilities, the Greenville plant is clearly differentiated from those of other materials players in the market by its focus on providing products of the highest quality that comply with ISO13485:2003 quality standards. Material Master Files of DSM products have been submitted to both the FDA and notified bodies in Europe.
While the materials you start with are critically important, of course, the ultimate market acceptance of a finished implantable device utilizing novel biomaterials rests on myriad factors, including how the material is processed.
A Best-in-Class Material Requires a Unique Processor
As a company that applies sophisticated processing techniques to the fabrics selected by MDCs for their new device projects, Biomedical Structures knows well how dramatically the commercialization prospects can be compromised when MDCs align themselves with those materials fabricators that don’t have the quality systems in place to support what will ultimately become the device history file for that product.
Biomedical Structures meets all the top-tier quality standards, including clean-room facilities, adherence to cGMP protocols, operation and validation to ISO 13485, high-level documentation, and other requirements necessary for a product’s regulatory submission and approval. Yet the contract manufacturer also has a key differentiator.
Unlike other processors that specialize either in R&D or manufacturing, Biomedical Structures offers a comprehensive suite of processing services to MDCs that support everything from the MDC’s design development and proof-of-concept stages all the way to full production. This approach represents a more complex and challenging business model, but Biomedical Structures believes, given the growing complexity of the quality and commercialization landscapes, that MDCs are better served this way.
Biomedical Structures’ unique position in the industry also underscores its commitment to the quality practices that ultimately support the needs of its end customers. By participating in all phases across the device development spectrum – from product conception to prototype development to manufacturing – Biomedical Structures helps customers eliminate the quality pitfalls that can occur when an MDC transitions from the R&D stage to product manufacturing. If one company supports an MDC through the product design and FDA approval processes and then the MDC enlists another company to manufacture the product, the MDC must bring the manufacturer through the entire learning curve of the design and establish all the appropriate quality controls to ensure the production of a quality end product. Because of the complexity of the process, critical elements can be overlooked during the transition, ultimately causing delays to the product release timeline or worse: quality issues that occur postrelease.
Creating Value through Quality
DSM, in fact, believes that quality management is not just an exercise in meeting regulatory checklists, but more importantly a core business responsibility that permeates the entire value chain. Manufacturers must gauge their customers’ requirements and plan their quality management approaches accordingly. For DSM, that entails understanding what the MDC wants and knowing how to translate that through the materials it supplies and the critical processes it employs. For DSM, quality management is not just about compliance – although that’s critically important – but also add value for MDCs.
Biomedical Structures is similarly focused on designing the quality approaches that provide long-term value for clients. For all the players in the medical device development cycle, the landscape is significantly more challenging than it’s ever been. But the need for innovative new devices that perform better and bring more cost efficiency into the healthcare delivery system is also at a peak point. Companies like DSM and Biomedical Structures, with their focus on quality and on supporting MDCs through this highly complex process, are doing their part to fuel the cycle of medical innovation and make way for the groundbreaking products and treatments to address unmet clinical needs and, ultimately, improve patient outcomes.
DSM Dyneema
9th Floor, Tower A, Infinity Towers, DLF Phase II
122 002 Gurgaon (Haryana) Ph : +91 (124) 417 9900