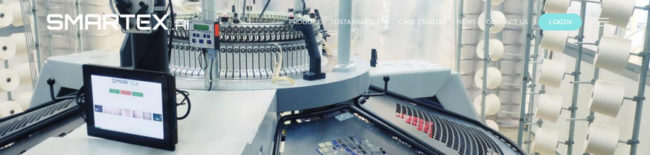
Smartex AI installation in North of Portugal at TINTEX Textiles knitting unit factory, in a Mayer CIE Relanit (open fabrics) machine
The textile industry is one of the largest in the world, worth more than 3 trillion US dollars across many stages of production. Unfortunately, textile factories produce a massive amount of waste and it is one of the highest polluting industries. This not only affects the environment but also impacts companies’ margins and the price of retail clothing.
There are several sources of defects throughout the textile production process But more than 80% of these defects happen during the knitting stage.
Knitted fabrics are produced on a Circular Knitting Machine. When the defects begin to be produced, they continue to be produced until someone intervenes. And many defects are smaller than 1 millimeter and almost invisible to the human eye. So these defects proceed onto the next stage of production.
Then, they are dyed and finished with expensive processes. They are often missed again and sent onto final garments. Defects at this stage are more visible and identified as an issue. Final garments are thrown out because of these knitting defects. Costing everyone a lot of money.
All of these companies have inspection processes in an attempt to minimize defects and losses. Many inspections are done by people, working day and night to spot defects. This is a difficult task for a person because most defects are impossible to be detected by the eye. Manual inspection is expensive and often fails to catch defects.
These faults are only perceived after quality control in later stages when they become more visible. The defects accumulate and propagate, becoming more expensive and increasing waste and financial losses.
|
SMARTEX solves this problem by identifying production defects at its earliest stage with a system of integrated cameras. By using Artificial Intelligence and Computer Vision to detect all defects and irregularities in real-time, it learns complex textile patterns and recognizes all the defects.
When a defect is detected, it alerts workers in real-time to intervene and prevent further faults. Smartex also provides production data for factory operators including real-time data on quality of production and tools that enable them to digitize their factories.
Smartex makes every knitting factory connected and increasingly automated. This will make the entire supply chain smarter, protect the environment from unneeded waste, and reduce cost and complexity for textile producers all over the world.
SMARTEX, the smartest way to produce textiles.
Smartex solution prevented mistakes in eco-knitted fabric
Turkey’s biggest fabric manufacturers EKOTEN Fabrics, improper production of circular knitting machine which reduces the rate close to 0% Smartex AI System uses. This new monitoring system contributes to the productivity and profitability of fabric manufacturers.
Smartex, pioneering in bringing the defective production closer to 0% in circular knitting machines, introduced the first and unique automatic inspection system, Smartex AI System, with improvements and innovations compared to the previous version. The AI-based system plays a big role in preventing defective production that is often not noticed right up to the painting stage and results in a huge waste of resources. Ekoten Fabrics, an affiliate of Sun Tekstil Group since 2020, invested in Smartex AI System to optimize the production process with sustainable technologies.
Acting in the direction of innovation and sustainability, Ekoten guarantees its customers 100% inspection and 100% traceability. For this purpose, the company took an important step by purchasing the Smartex AI System to support its production team. EKOTEN Director of Operational Excellence Mystery Plays, volume of business, saying that Turkey and internationally in sustainable development mean that they can make an important contribution; “We know that the Smartex System will help us on the way to a sustainable future. For us, it is very important to monitor our production as well as prevent fabric waste. “Smartex definitely solves these problems,” he said.
100% traceability for 0% error with Smartex AI System
Smartex achieved strong market development in different countries throughout the year 2020. Main activities in Europe decided to continue the company’s largest market is accounted nearby Turkey. Since the fall, more than 30 of the current V1 version have been sold and installed; hundreds of them are already in operation. Among the highlights of this version are detection enhancement, the ability to work with limited bandwidth, and the online platform that allows production monitoring.
According to the feedback received by Smartex from its customers, the savings achieved in raw material with the interventions made by the Smartex V1 System is an average of 10 rolls per machine per month. The Smartex camera system is the first and unique solution that enables 100% inspection in circular knitting machines to reduce faulty production to approximately 0%. This system; Detects defects such as elastane streaks / dashes like lycra, oil stains / streaks, multiple size holes down to sub millimeter, continuous or interrupted thick thread / thin thread In addition, Digital Roll Quality Reports and Roll Defect Coordinates Map are offered for online quality control. This platform allows mills to share digital versions of fabric rolls with their customers and see real-time machine performance.
The only way to sustainable production is to optimize the production process
Smartex Head of Communications and Partnerships Ana Tavares said this technology was developed as a market solution to a hidden problem in the textile industry. What defines this as the lack of quality and traceability that causes a large amount of textile waste; “Every textile factory is dispatched from traditional production to a more sustainable production. What does it mean? For a long time it was enough to use only recycled raw materials. Today, the industry understands that the only way to get there is to optimize production processes, at this point technological companies such as Smartex play a very important role, ”he said.
Smartex Head of Business Development Rui Pereira, on the other hand, stated that existing customers realized the advantage within a few weeks after the installation. Pereira; “This is 2021 and we are currently Portugal, in markets such as Italy and Turkey are the things that we trust will be a significant year in terms of sales both in new markets,” he said.
Courtesy: Textilegence, Turkey, and